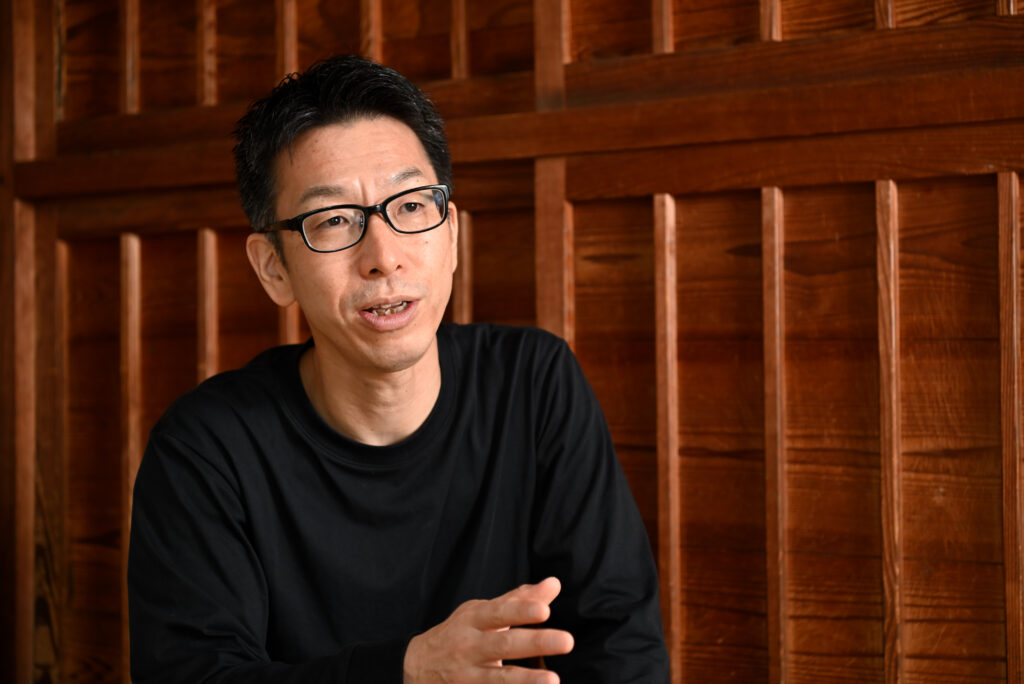
Yabushita: I am currently studying industrial districts and clusters at the graduate school of Fukui Prefectural University. Your thoughts on the production area remind me of the cluster theory suggested by Michael E. Porter. A cluster is defined as a group of companies and institutions that are located geographically close to each other. He stated that clusters generate three main advantages in competition. One is that innovation supports the growth of productivity. He claimed that the existence of competition between local companies and competition is essential for developing innovation. (On Competition Updated and Expanded Edition, Michael E. Porter).
The companies are both friends and rivals, and that kind of ambivalent relationship is generated by a closely located environment such as a cluster. I think it is one of the factors that structure a cluster, and that relationship cannot be developed with only one winner. The development of the lacquerware industry in the Katayama region, which is rich in diversity, may have been triggered by active innovations due to clusters of immigrants.
Komamoto: Another driving force toward education is the desire to spread our unique Japanese lacquer decoration culture, such as “Maki-e” and “Chinkin .” Lacquer coating culture was developed in other countries as well, but traditional Japanese “Maki-e” excels above all others. I believe it’s a highly developed lacquer decoration culture that is the one and only; even China and Korea do not have this. We would like to convey and grow the advantage of the unique handicrafts that cannot be reproduced by machines, wouldn’t we?
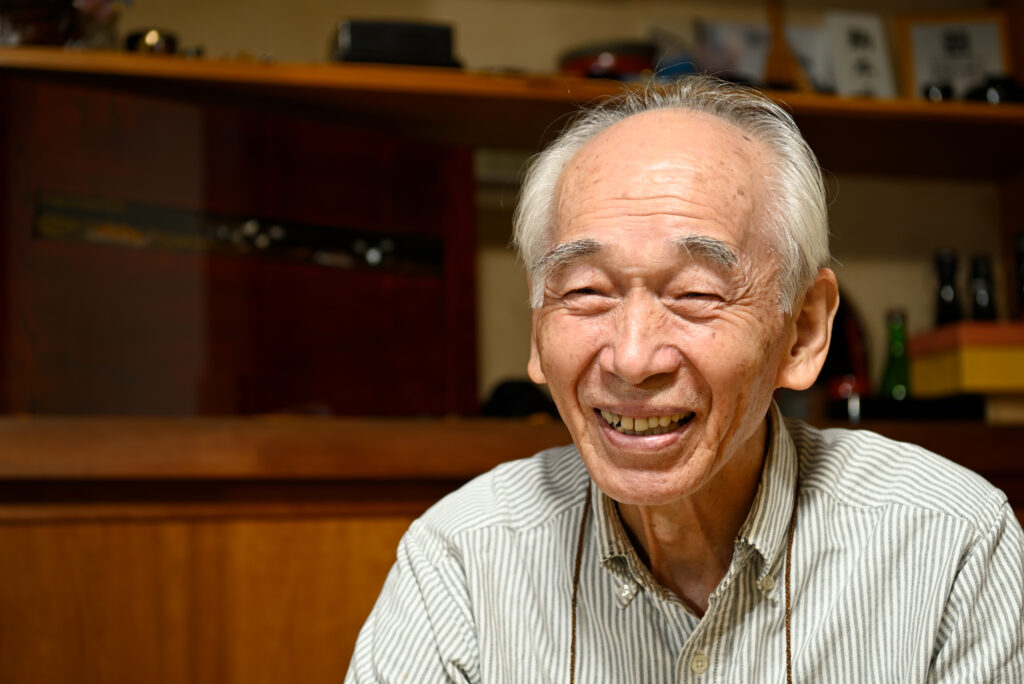
Koharu: Yes. I have been strongly attracted to handicrafts. I have liked painting since I was in elementary school, and I have been interested in traditional crafts, also. When I was looking for a job in my third year at university, I thought about what I really wanted to do. Echizen lacquerware came to my mind first, and then I was introduced to you, Mr. Komamoto.
Mr. Komamoto supervised my lacquer painting for three weeks during summer vacation, and I found that I was thoroughly absorbed in the precise and delicate work. In addition to that, I was also impressed and surprised by how the natural material of lacquer allowed me various expressed and attracted the Kawada area, where craftspeople who could use lacquer expertly existed a long time ago. During the training period, I knew that the number of Maki-e craftspeople was dwindling year by year. There were no craftspeople in their 20’s or 30’s. I wanted to learn this technique born in that area at any cost, and I asked Mr. Komamoto to accept me as an apprentice.
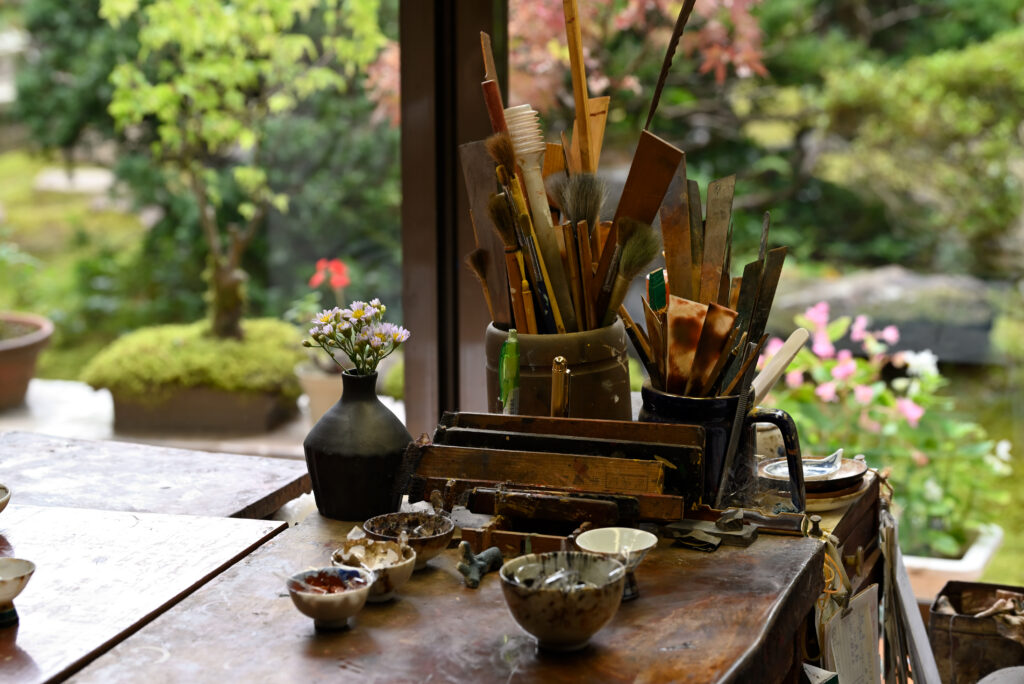
Yabushita: I have been interested in manufacturing, including sake brewing, for a long time, and I have been involved with much traditional manufacturing in my neighborhood, both professionally and privately, since I worked for a sake brewery. In such an environment, my daughter, Koharu, started her Maki-e training under Mr. Komamoto, and I had a connection with Mr. Komamoto. I became aware of the existence of Kintsugi at that time. I was surprised by the power of lacquer when I looked at the exhibited tea ceremony pot repaired with the Kintsugi technique at the “Beauty of Tsukuroi (repairment)” exhibition held at the Atago Tea Ceremony Museum. The bottom of the pot was repaired with a mixture of lacquer and iron powder, Kana-urushi (iron lacquer).
After that, I studied lacquer. I was fascinated by the power of lacquer, a natural material that works as paint and adhesive glue. Now, I want to be a Kintsugi craftsperson. Mr. Komamoto, you may think, “Why would the father of my student disciple want to become my student disciple?” Your passion for spreading the charm of lacquer to the world is the same as mine. Exhibitions and competitions are important events from a popularity standpoint because people may know about lacquer manufacturing through the events, I believe.
Mr. Komamoto, you received many awards, including the Order of the Sacred Treasure Silver Rays and the National Lacquerware Exhibition, and which is the most prestigious?
Komamoto: The most prestigious award I’ve received is the Fukui Prefectural Governors Award, the highest award at the Echizen Lacquerware Exhibition. I was happy that I received this award two years in a row (2016 and 2017). I am more impressed by this award than the Japan Lacquerware Association Chairman’s Award at the national lacquerware exhibition and the award of the Order of the Sacred Treasure, Silver Rays. I think my technique was highly evaluated compared to the other craftspeople. We know each other well in this manufacturing area, so I was happy and proud of it.
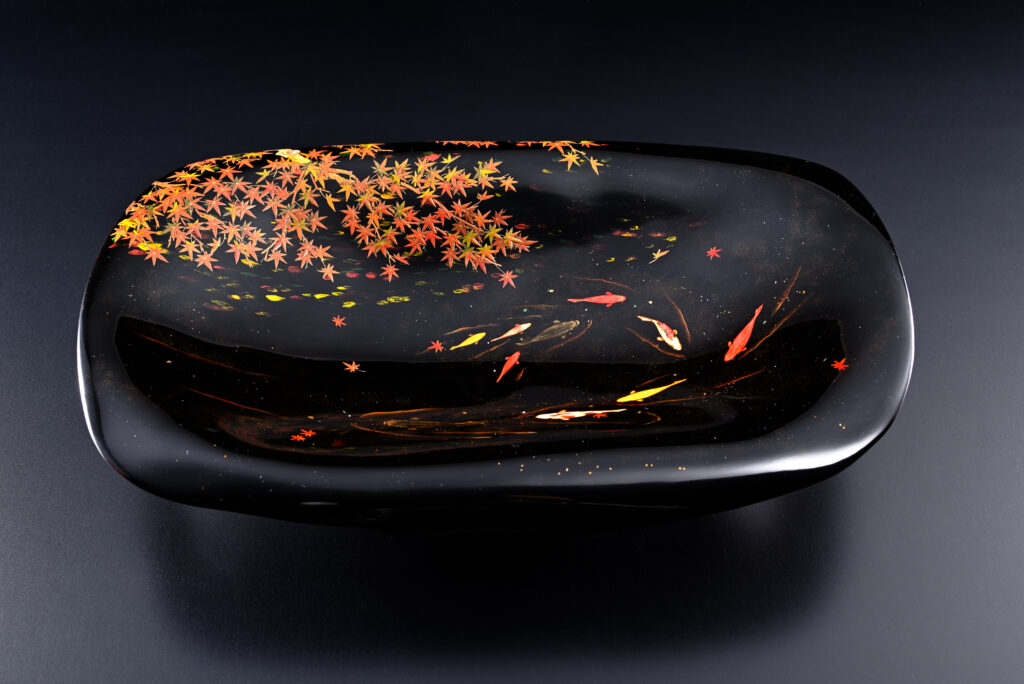
Awarded the Lacquerware Association Chairman’s Award (2021) at the 56th National Lacquerware Exhibition in Japan.
Yabushita: Koharu, you received the Echizen Lacquerware Exhibition Prefectural Council Chairman’s Award for the first time. We can’t compare the value of the prize with the ones our master, Mr. Komamoto received, but how do you feel about it?
Koharu: I have not done all the procedures, for example, the preparation of lacquer, so I think I shouldn’t be arrogant. However, I competed among the craftspeople in this manufacturing area and won the prize. Therefore, I am glad to receive the award. Those two feelings exist in my mind at the same time. Mr. Komamoto has been suggesting applying to competitions and exhibitions, and I have been doing so since last year. I could find the meaning of the application recently. Awarding prizes motivates me to continue manufacturing.
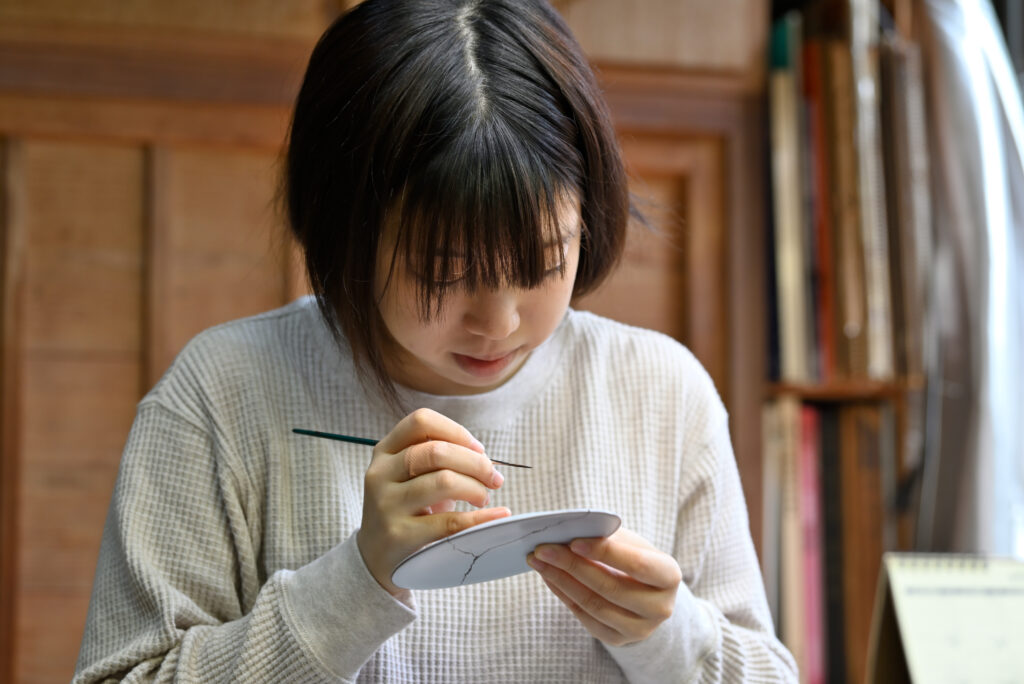
Yabushita: We learned lacquer techniques from Mr. Komamoto, and now I established a lacquer factory, Urushi no Komaya, giving part of Mr. Komamoto’s family name, “Koma .” Mr. Komamoto, could you give me well-wishing words for me to congratulate my factory?
Komamoto: I am honored that you included part of my family name, and it will live on. I am very happy. I have wanted someone to inherit my work since the Komamoto family as a lacquer manufacturer will end in my generation. I feel like my lifelong dream has come true. People may think that Maki-e work is unspectacular. I believed that people would recognize the worth of my work someday, and I put up with the work steadily in an honest way.
“If you do a good job, the beauty of lacquer will surely resonate in people’s hearts.”
Please keep manufacturing with your best effort.
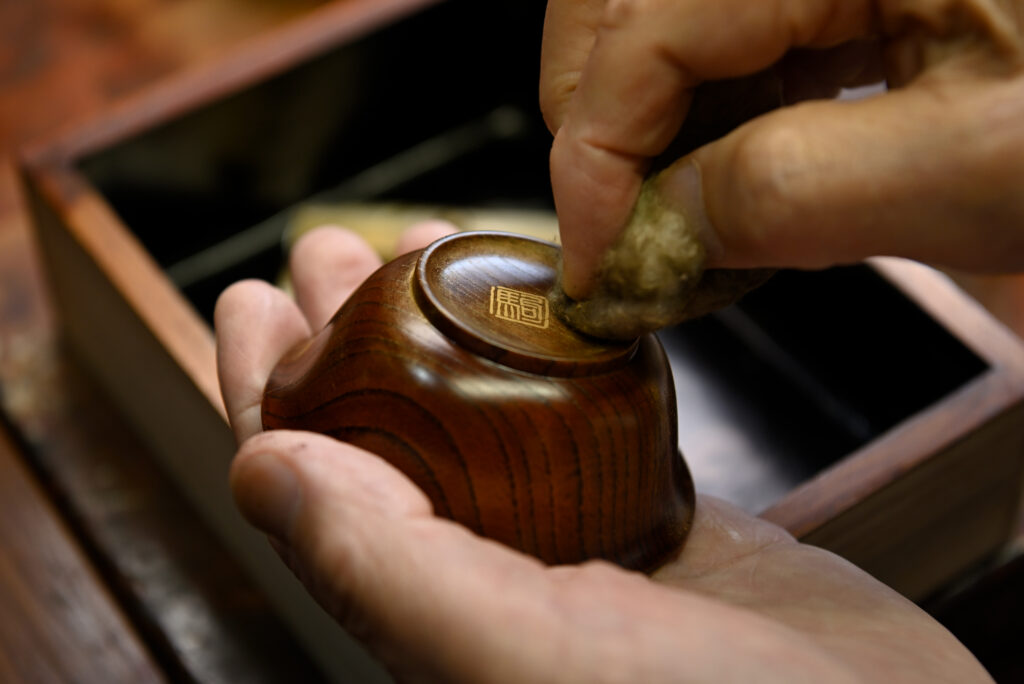